- Static electricity: the confinement of excess charge.
- Static charge on personnel.
- Charging of material.
- Removing or avoiding charge on materials.
- Attraction/repulsion–unintended static forces (e.g., contamination) and intended forces (pinning).
- Electrostatic spray painting, powder deposition.
- Surface conductivity– measuring “ohms per square”, and making surfaces more conductive.
Static Electricity is the confinement of excess charge: When an excess of either positive or negative charge is confined into a relatively small volume (far from any excess charge of the opposite polarity) mutual repulsion occurs between the charges within that volume. This repulsion causes the charges to try to leave the confining volume and fly apart, releasing energy. This energy is available to do damage by sparking. If two neutral but dissimilar materials are rubbed together, causing one to become + and the other -, there will be very little repulsion energy available on either object while they are close together. Only when they are separated will a significant of “spark” energy be stored on each object. In addition to sparking, charged objects may be attracted to each other (or repelled). There is always an attractive force between uncharged conductors (such as sheet metal or even individual dust particles) and charged objects (such as an insulating surface that has just had adhesive removed from it). A more detailed explanation of the mechanisms of static electricity can be found here. There are several situations that produce unwanted static electricity. The causes and solutions will be discussed by category below.
Personnel becoming charged: High static voltage on people is (of course) most commonly caused by rubbing dissimilar materials together. This type of charging is called the “triboelectric effect”, and a table of materials and their relative charge is here. A common example of triboelectric charging occurs when rubber-soled shoes rub against nylon carpet. Some electrons jump from the nylon to the rubber while the two materials are in contact. As the person walks across the carpet, more electrons accumulate on the bottom of the soles. The mutual repulsion of these electrons becomes very strong, especially while the shoe is lifted away from the carpet (away from a significant amount of + charge, which remains behind on the carpet). With strong repulsion, some electrons move off the sole and up to the person, because rubber is not a perfect insulator. Also, some electrons actually spark through air from the sole up to the person. Therefore the person acquires an increasing negative charge. Being a “conductor”, the person can rapidly discharge most of the energy all at once. If the person brings a finger close to ground, most of these electrons will spark to ground at that location.
“Shoes on carpet” is am example of two insulators exchanging charge. This type of charging can also occur if a conductor (or even human skin) is rubbed against an insulator, but it does not occur when a conductor is rubbed against another conductor. The charging can be reduced by limiting the environment to materials that do not charge very much (see the triboelectric table). In general, materials with an affinity near zero (e.g. cotton, nitrile rubber, polycarbonate, ABS) will not charge much when rubbed against metals or against each other. Other materials will charge much more, such as urethane foam and clear carton-sealing tape (both strongly +), or teflon and most types of rubber (both strongly -). Human skin will charge (generally +) when rubbed against insulators, but skin is a conductor so it will not charge when rubbed against other conductors. Charging problems can be greatly reduced by proper selection of materials, such as cotton, ABS, etc,, and by using work surfaces that at least weakly conduct electricity (i.e., are antistatic so that personnel do not charge when they touch the surfaces).
In most situations, personal grounding devices (wrist or footwear ground connectors) work very well to reduce body charge and voltage to safe levels even when significant charging is present. However, both for personal safety and to reduce high-current surges, a resistor is constructed into the assembly, in series with the ground. Its value is usually selected between 100,000 and 10 million ohms. This resistor allows the body voltage to spike if a spark, ESD event or current spike occurs to the body. In addition, a persistent AC or DC body voltage, which will be inversely proportional to the selected resistance value, will appear if a current source is present. Current sources include the proximity to an AC or DC ionizer, triboelectric frictional charging (current is present only during the act of rubbing), or accidental touching of a voltage source, even if low voltage (hand-to-metal resistance is generally less than the resistance built into the ground connector). If there are problems with personal voltage exceeding allowable limits, even momentarily, reduce the grounding resistance. (A personnel voltage touch monitor can be used to identify the sources of such problems and whether the resistance is correct for a given application.)
Material becoming charged: Static charging of material is not inevitable– it is a process which can be interrupted at various stages. An example of (possible) static charging is a continuous sheet of paper passing over a natural rubber roller, as shown below.

Although the rubber roller (black) is shown with “-” charge on its surface, assume that both the roller and the long paper sheet (gray) were uncharged before they came into contact with each other. The “beginning” of the paper sheet is shown in the right side of the image; note that it has acquired a lot of + charge as a result of its contact with the roller, whereas the rest of the paper has less charge or none. When paper is rubbed against natural rubber, the surface of the rubber takes electrons from the paper, thus becoming negative. The paper therefore becomes positive. However, there is a maximum amount of – charge the rubber surface can take (about two one-billionths of an amp-second per cm2). Then the rubber cannot remove any more electrons from the paper. If the system is exactly as shown above, then after the first few feet of paper pass over the roller, the rest of the paper will not be charged by the roller. In this idealized example, the static problem quickly disappears.
In the real world however, the design of the system will generally cause charge to continue to accumulate on the paper. This occurs because charge leaks off the roller and/or is directly deposited onto the paper. If the charge on the roller is allowed to flow to ground, then the roller can continue to charge the paper indefinitely. Many rubber parts contain some carbon, which makes them slightly conductive (antistatic). This property may seem like a good thing, but it is bad in this case. If the bearings on an antistatic rubber roller are metal and grounded, then the excess electrons can flow to ground, allowing the roller to continue to charge the paper. In effect, electrons are removed from the paper (by the roller) and then have a route to ground, instead of being trapped on the roller. If charging occurs via this method, switching to pure (not carbon-filled) rubber or isolating the bearings from ground will reduce the problem, but these steps could cause other problems. By far the best way to reduce charging is to use a roller made of material that does not charge paper very much. By consulting a triboelectric table, it becomes clear that nitrile rubber is a much better choice than natural rubber for a paper roller. Note also that if natural rubber becomes highly charged, its surface could spontaneously spark, allowing some of the electrons to escape into the air. This will allow the paper to begin charging again. Sparks are more likely if metal is nearby. If contrast to natural rubber, nitrile rubber against paper is not likely to charge enough to spark.
If grounded metal parts are placed near the roller (or near anything that is already charged), they may cause additional charging. Shown below is a metal rod (blue) which is electrically connected to earth ground. The rod may be a brake or a speed reducer; however, it also removes the – charge where it touches the roller. (Assume the rubber is not antistatic, but is instead a perfect insulator, and ignore any friction charging that may occur as the metal rubs the rubber.)

Now the paper becomes uniformly and strongly charged, and charging does not eventually stop. (Generally, a rounded rod as shown will not remove all the charge, as is implied in the picture. A sharpened knife blade will remove more charge than a rounded shape will, and grounded “tinsel”, which is often used to remove static charge, removes even more. Sharp metal pieces can remove charge as shown above even if only close to the roller but not touching it.) Ironically, just as in the previous example, this removal of charge from the roller makes the static problem worse.
In addition to the removal of – charge from the roller by metal touching or near the roller, the paper can also acquire a + charge if metal parts are near the paper. The picture below introduces a sharp metal knife edge (blue) which is grounded. “Tinsel”, which is composed of thin strips of metal foil, will have the same effect as the knife blade.
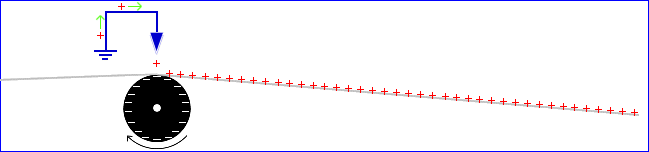
When a sharp piece of grounded metal is held near a sufficiently-charged object (the roller), the opposite charges will shoot out of the sharpened point and these charges try to collide with the charged object. Instead, the paper gets in the way, and the paper receives the charge. As can be seen, attempts to neutralize the static (in the picture by using a knife blade) can go terribly wrong if not applied in the correct way. Similar charging will occur if a top roller is added, provided that it is grounded metal. If the knife blade is moved to the right (by a distance of a few times the roller diameter), then the blade can finally do some good, because it can remove some charge from the paper.
Removing or avoiding charge on materials: If the material is a good conductor like metal, touching it to ground for even a brief moment will discharge it. This should only be done if the conductor is not close to a highly-charged object or a to metal sheet that is at high voltage. If too close to such an object, the conductor will pick up significant charge by charge induction the instant any part of the conductor is connected to ground. That charge will be of the opposite polarity of the charged object, and the conductor will carry this charge until it is discharged properly, away from any such charged objects. (The conductor will also pick up induced charge if it is “discharged” by an AC ionizer while near a charged object.) Remember however a conductor that is properly discharged can still attract charged dust of either polarity because of the “image charge” effect. Therefore it is also important to remove any charge from dust in the air if there is a contamination problem. (Image charge effect: a dust grain that is for example + will be attracted to a neutral metal surface because the metal creates an electric field that pulls the charged dust toward it. The pull force is the same as if the metal were a mirror and the + dust grain “saw” the reflection of an equal but opposite – dust grain in back of the metal surface.)
An insulator is more difficult to discharge than is a conductor. However, many “insulators”, like paper or glass, are slightly conductive. These materials can be called “slow conductors“, and a ground connection will discharge them it is if held in place for a while. For uncoated paper, the time required to discharge a linear foot is roughly one second at 40% humidity, and is faster at high humidity. Passing the entire width of the roll over a grounded wire or rod will work well if the linear speed is low enough (at 40% RH, a speed of about one foot per second or slower will work) or if the humidity is increased, or if several successive rods are used. When discharging a conductor by using a grounded metal piece, the metal piece does not have to be sharp (a knife edge). All that is needed is actual contact with the metal piece. Regardless of whether the metal is sharp or smooth, a conductor will be fully discharged if held in electrical contact with ground for a long enough time (“long enough” ranges from nanoseconds for copper to seconds for paper).
When using a grounded metal piece to discharge insulating material (known as a “passive” discharge method), the optimal configuration is slightly different. Rubbing rigid metal against an insulator can actually charge the insulator. A slow conductor like paper can also charge when rubbed against metal, if the rubbing and separation are done rapidly (in less than typically one second). The triboelectric table contains additional information. The best passive method of discharging an insulator is the use of grounded tinsel. If a continuous-feed sheet of plastic is to be discharged, thin foil (tinsel) or thin wires gently touch the plastic, connecting it to ground as it travels by. The spacing between tinsel or wire points should be 1 mm or less for maximum discharge efficiency. Even though the points may actually touch the plastic, the frictional force is negligible when using tinsel or thin wires so that there is little additional charging due to metal-to-plastic rubbing. This method cannot remove all the surface charge on the plastic. If tinsel is set up properly, the surface charge can be reduced to around 2% of the maximum possible surface charge (maximum charge before spontaneous sparking is about 10-9 ampsec per cm2.) An electrostatic voltmeter (surface voltmeter) will typically read about 500 volts when this best-case 2% is achieved. Paper is slightly conductive so it will discharge passively more completely than plastic will, especially ay low feed speed and high humidity. The initial reduction to 2% is instantaneous both for plastic and paper; further charge reduction is gradual for the paper. (For plastic, no additional charge reduction occurs, even at high humidity. However, if condensation occurs, plastic, as well as any other material, will instantly discharge completely.) Instead of tinsel or fine wires, engineering constraints sometimes require that a rigid metal structure be used to discharge a moving insulator sheet. If so, the metal should not touch the sheet because of the possibility of frictional charging. The metal should be a grounded knife blade that is spaced between 1 and 5 mm from the sheet (the “knife” is oriented perpendicular to the feed direction and covers the entire sheet width). As an alternative to a knife blade, a row of grounded metal needle points can be used. Typically the points are 5 mm apart and are 5 mm away from the sheet. These non-contact discharge devices are slightly less effective than tinsel and become less efficient if the points are dirty of dull.
Active discharge methods: Remember that passive metal structures cannot fully discharge an insulator, but passive methods may remove enough charge, depending on the requirements. Other methods can fully discharge insulators, but these methods all require some sort of energy. For example, air becomes a reasonably good conductor if a large number of both + and – ions are present, but energy is required to make air ions. Usually, ions are made by using either electricity or radioactivity, but they can also be made from combustion, high heat, or evaporation. If 100,000 ions per cm3 (both + and -) are present in air, charged insulators will discharge to half their initial value (half life) in about a second. (Formulas are here). High ion concentrations can only be achieved by using an ionizer; without this, a room has typically 10 to 100 ions per cm3, which corresponds to a discharge half life of tens of minutes to a few hours. (Perfect insulators, if charged, will discharge with this half life while in the room. If a material is somewhat conductive, it will discharge faster.)
The low-tech way to remove charge fully from an insulator is to dip it in (grounded) water, or breathe on (or humidify) the insulator until condensation forms, making sure the water film has no gaps and that it bridges to ground for at least an instant. Then any excess water on the insulator can be shaken off, and it should be air-dried (high-pressure and/or heated air is OK) to remove the water. Do not wipe, because this action will charge the surface.
A more technical full-discharge method uses an ionizer. If a large number of both positive and negative ions coexist in the air, the positive ions will be strongly attracted to negatively-charged surfaces and vice-versa. Each ion transfers its charge to the charged surface and then the ion falls apart, turning back into various air molecules. The attraction and charge transfer continues until all surfaces are neutralized. The most common ionizer is the AC electric type, which is made from one or more sharpened needles connected to several thousand volts AC. If the charged surface or object is passed under this AC ionizer, all surface charge is quickly removed because positive and then negative ions are produced with every AC cycle. (If the object is a thin film, even charges on the far side, away from the static eliminator, are effectively removed). There are some problems with the range (effective distance) of an AC ionizer because the very high concentration of co-existing + and – ions near the electric needles. Oppositely-charged ions tend to collide and thus destroy each other so that the concentration is high only within about one foot (30 cm) from the needles. This is roughly the distance + or – ions travel within a half of the 60 Hz cycle. For this reason, “DC” ionizers are also manufactured for antistatic purposes. DC ionizers actually switch between + and – only a few times a second and thus have a longer distance range. However, this DC type will create higher (+ then-) transient voltages on surfaces than AC ionizers will; if an object is passed near a DC ionizer and then removed quickly, the object may have residual charge of the same polarity that the ionizer was emitting at the instant of removal. The range and effectiveness of an AC ionizer can be greatly improved by adding a fan (see below for more explanation). In addition, an AC ionizer used with a proper fan will discharge objects smoothly, without voltage transients. Several companies make AC and DC ionizers, including Exair and Amstat.
An electric ion source obviously cannot be used in an explosive atmosphere. However, ionizers can also be made from radioactive material (usually the elements Po or Am). Energy is required to make ions, and the alpha particles that come from these sources can each produce about 50,000 pairs of (both +and -) ions as they travel a few centimeters in air before coming to a stop. (Then each alpha becomes a non-radioactive helium atom.) These nuclear ionizers produce far less energy per alpha decay than 0.00001 watt second (0.01 millijoule), which is approximately the minimum, energy to detonate even the most sensitive fuel-air mixture. (Each alpha has about a trillionth watt second of kinetic energy). This 0.01 millijoule is called the “Minimum Ignition Energy” (MIE), and the value varies with the type of fuel. There are no known harmful effects from these nuclear ionizers if you are more than about one foot away, and they use the same isotopes as in common smoke detectors.
Any hot surface (like an electric strove element that is at least not enough to glow noticeably if the room lights are off) will emit large numbers of both positive and negative ions, so a stove element or electric “burner” can also be used to discharge surfaces. However, the energy requirement is quite large, so this method is not common.
A fan greatly improves ionizer performance. When using AC electric or radioactive ionizers without using any air circulation, the object being discharged must pass close to the ionizer. If the ionizer is more than about a foot (30 cm) away from the object, then a fan should be positioned near the ionizer. It should blow air perpendicular to the direction that the ions normally exit the ionizer (the front of the ionizer), and the main air stream should include the region from the front of the ionizer to 30 cm in front from the ionizer. The air should be directed so that it reaches the object within about two seconds after passing the ionizer. It is also important that the object lingers within the high-ion region for a long enough time to discharge. If the surface is a film driven by a conveyer belt, the belt may need to be slowed down if sufficient discharge is not taking place, or more ionizers can be added. An air ion counter can be used to determine if the ion distribution is optimized. Discharge half life is inversely proportional to the number of ions per cm3, so this type of measurement allows rapid determination of discharge time. Another tool used for antistatic optimization is a surface voltmeter, which measures the charge on materials, as opposed to detecting ions in the air.
Attraction/repulsion–unintended static forces (e.g., contamination) and intended forces (pinning): If dust floats near an object at high voltage (highly charged), the dust will usually be attracted and then will often stick to the object. This behavior may seem counterintuitive; opposite charges attract, same charges repel, and by extension, an uncharged dust grain should be unaffected by a charged object. Furthermore, even if the dust touches the object, we might expect the dust to acquire some of the charge from the object and therefore be repelled, not attracted. If fact, surfaces that have very high charge (near spark potential) do directly charge some of the dust grains that touch the surface, and then repel those grains (at a high speed). At somewhat lower charge, virtually all dust that touches the surface will stick. If the surface voltage is reduced to < about 500 volts (as read on a surface voltmeter), the tendency to stick becomes independent of the surface voltage, and is instead caused only by typical atomic (van der Waals) forces.
In order for uncharged dust to have dual attraction both to + and – surfaces, dust must be at least slightly conductive. (In contrast, floating plastic particles will only be attracted to a charged surface if the plastic and surface have opposite charges, because plastics are good insulators.) Dust that comes near a + surface will be attracted to the surface because the dust becomes electrically polarized. That is, some of the electrons in a dust grain can move around inside the grain. These “free” electrons will move to the part of a dust grain that happens to be closest to the + surface, leaving the far side of the grain with excess + charge. Because the – charge in the dust grain is closer to the charged surface, its attractive force (toward the surface) is stronger than the repulsive force of the + charge on the far side of the grain. Therefore the grain moves toward the surface and (eventually) will usually touch it. Note that if the dust grain is long compared to its diameter (i.e., a fiber), the grain will orient itself (by a simple rotation) so that the long axis becomes perpendicular to the charged surface.
If the surface is very strongly charged (over 20 kV on a surface voltmeter), most of the attracted dust particles will never actually touch the surface. Instead, when the dust gets close, the + surface will send out a + spark. This charges the dust + and it will immediately fly away at several hundred cm per sec, although a minority of dust grains will touch the surface. If the surface charge corresponds to between about 500 V and 10 kV, almost all the dust grains nearby will eventually touch the surface, because the surface does not directly spark and thus repel them. However, a spark can be emitted by the far side of the dust grains. This happens when the dust grain’s near side is touching the + surface; the far side immediately sends out a + spark. This sudden loss of + charge gives the dust a – charge, so it sticks to the + surface. At voltages < about 500 V, there is not enough charge for the far side of the dust to emit a spark, and the polarization force that brought the dust there is relatively weak. The dust may adhere to the surface, but mostly due to atomic forces, which are present whether the surface is charged or not. If there if air movement the dust may rub against the surface, which causes it to stick due to triboelectric charging.
If a charged insulator surface is discharged as well as is possible by using a passive method (grounded tinsel or a sharp metal shape), there will be relatively few contamination problems caused by static electricity. (Make sure the surface reads under about 500 V with a standard electrostatic voltmeter (surface voltmeter) to verify effective passive discharge. Note also that technically an electrostatic voltmeter reads charge per area on an insulator, not actual voltage. The distinction is not critical, but further clarification is here.) Even at this low charge, there will be a weak polarization attraction of dust, but the strength of this attraction is proportional to the square of the surface voltage. At 500 V, the attractive force that a given dust grain will experience is 1/400 of the attraction at 10 kV. Charged plastic (or any insulator) powder poses a different problem. If the plastic powder is of opposite charge as the surface, powder will be significantly attracted to the surface even at < 500 V. Attraction in this case is directly proportional to the surface voltage. With charged powder present, the surface needs to be fully discharged (as above) or even slightly charged with the same polarity as the plastic powder.
A metal surface that is held at high voltage will attract dust in the same way that a charged insulator surface will. In addition a grounded (uncharged, V = 0) conductor will attract both (conductive) dust and powdered insulator if they are charged. This is due to the “image charge effect”, in which a dust grain that is for example + will be attracted to a neutral metal surface because the metal creates an electric field that pulls the charged dust toward it. The force of attraction between dust and an uncharged metal surface is the same as if the metal were a mirror and the + dust grain “saw” the reflection of an equal but opposite – dust grain in back of the metal surface. The attractive force is proportional to the square of the amount of charge on each grain, which is difficult to measure directly. (To measure the charge per dust grain using the Surface DC Volt Meter USSVM2, allow some grains to accumulate for several seconds on the sensor, which is essentially a grounded conductor so it will attract charged dust. Then note how much the display voltage changed during that accumulation time. Each volt represents a charge of 0.3 pC [3×10-13 amp sec]. Use a lens to count the number of dust grains captured and then divide the total charge by that number to obtain “Q”, the average charge per grain in C or ampsec. If the distance between the dust grain and the metal is X, then the average attractive force at that distance is 2.2×1015 Q2/X2, in grams.)
Ionizers can remove the charge from charged dust and charged insulator powder, and AC and radioactive ionizers work much better than DC ionizers in not leaving a residual charge on the dust. Remember that charged dust or charged insulator powder will be attracted to grounded metal, and strongly attracted to metal held at voltage of the opposite polarity as the dust or powder, and also to insulator surfaces charged with that polarity. In an ion-enhanced environment, the charge half life of dust or powder is difficult to measure directly. However, the half life can be determined by measuring the number of ions per cm3 with an air ion counter. (Half life in seconds is 1.2×105 divided by the number of ions per cm .) It is best to set up the ionizer(s) so that dust remains in the ion-enhanced zone for at least 10x the charge half life. Ionizers will also discharge insulator surfaces at the same rate.
The attractive/repulsive force between two intentionally charged surfaces can be predicted or measured by several methods. By adding charge appropriately, a plastic bag can be forced closed on an assembly line, or two materials can be prevented from touching each other. If designing a system where charge is added by rubbing, the triboelectric table can be used to determine how much charge is transferred as a function of both friction energy and which dissimilar materials are used. If one of the two “dissimilar materials” is part of the conveyor, some charge may need to be removed from it or added somewhere else, as shown above in charging of material. In addition to friction charging, a “pinner” can be used. This is an ionizer that produces only – or only + charge, and can rapidly charge a surface that passes nearby (charging usually takes only a fraction of a second). The ions from the pinner must be moving at high speed in order to overcome the repulsion of similar ions on the surface that had just arrived milliseconds before. Generally the surface should pass within about 2″ (5 cm) from the pinner. Slightly longer pinner-to-surface distance can be used if the back side of the surface that needs charging is near a ground plane (a metal sheet connected to earth ground). If the surface is being charged positive for example, then negative charges in the ground plane will be attracted to near the back side of the surface that is charging. The number of + charges per square inch in the ground plane will be almost as many as the – charges per square inch on the sheet. Therefore, the + ions being emitted by the pinner will not be repelled significantly, and they may be able to travel typically as much as 10″ (25 cm) to the surface. It is common to use a + pinner on one side of the opening of a bag, and a – pinner of the other, so the bag will close itself and stay closed.
The forces can be measured directly with a gram scale to verify if they are within specs, although this method has some shortcomings. The force is usually weak and technically difficult to measure. If one surface is charging properly but the other is not, the force will be zero, but a scale cannot determine which surface is improperly charging. An easier way to determine the force is by measuring the charge on each surface and using a formula (the method is discussed here). When using an USSVM2 surface voltmeter to measure the charge on one sheet (displayed as V1), and then on the other surface (V2), the force per area in grams/cm2 is 7.5×10-11 x V1 x V2. It is attractive if V1 and V2 are of opposite polarities. The output charge per area of a pinner can be measured directly using an ion current meter. This can determine proper placement and whether the output pins of the pinner need cleaning. (Output decreases if the pins need cleaning, which is typically after a few days of operation, but it is more frequent in a dusty environment.)
Electrostatic Painting, Powder Deposition: In these deposition processes, a powder (or sometimes a liquid) is atomized and given an electric charge. The charged particles of powder drift toward a conductive workpiece (the item that is being powder painted), usually with additional airflow assist from a fan or pump. The powder is electrostatically attracted to the workpiece and sticks to it. Then the workpiece is heated, which melts the powder so that it forms a smooth, solid coat. Heat (or UV for a low-temperature piece such as wood or plastic) will also polymerize the melted powder if the coating is permanently-hardening (a thermoset).
There are two main systems or types of electrostatic powder deposition. The more common is the “corona” type, which blows the powder or liquid particles out a nozzle and then charges them after they leave the gun, by spraying them with ions. The ion source is a needle that is held at very high voltage–as high as 100 kV. It is usually at the front of the nozzle and it sprays charge forward and radially outward. (Sometimes the ion source is far from the nozzle, especially if the back side of the piece needs coating.) The applied voltage is usually negative, but it is positive for nylon and some other materials, because each material has its own charging preference. (See the triboelectric table for more information.) In addition to adding some charge to the powder, a much greater amount of charge is added to the air, forming a (usually negative) wall of ions 20 to 30 cm in diameter. This wall strongly repels the now-charged powder, which is located between the ion wall and the conductive workpiece. Because of the “image charge effect” (see the attraction/repulsion section above), the piece acts as though it has the opposite (usually positive) charge as the ion wall, so the piece strongly attracts the charged powder. Because of the nature of the image charge effect, the attraction is stronger on the edges of the workpiece, weaker on flat regions, and very weak at a concave surface or crater on the piece. This effect causes thick coating on the edges and very thin coating inside holes. With a corona system, very little of the powder misses the piece, but the coating thickness may not be uniform.
The other system is the “Tribo-gun”, which charges a powder (cannot be used with liquid paint) by “rubbing” it. The powder travels through a long tube usually made of teflon, which is the most electronegative of all common materials. (See the triboelectric table.) Teflon takes electrons away from virtually any material that rubs against it, so the teflon becomes negative while the powder becomes positive as it rubs against the inside of the tube. The negative charge that the teflon acquires is continuously removed and that charge is usually measured with a microamp meter. The powder is propelled through the tube by compressed air. When it leaves the tube and travels toward the workpiece, there is no “wall” of ions (as there is with a corona system). Consequently, there is relatively little electrostatic repulsion to repel the charged powder away from the tribo-gun nozzle and relatively little image charge effect to attract the powder to the workpiece. The powder is instead blown to the workpiece by air movement. Then each powder particle that comes within about 10x its own diameter from the workpiece (i.e., less than a mm away), will be attracted to the surface by its own image charge. Once it touches the workpiece, it stays there because its charge does not usually leak away to the workpiece. However the charge does leak away if the powder is at least slightly conductive. If the powder is contaminated in this way, it will fall off soon after being deposited. If conductive powder is used for coating, it should therefore either be made slightly sticky or be sprayed onto the workpiece while the workpiece is hot, so the powder will melt on. (The conductivity of a powder can in theory be measured before deposition by using a high-resistance ohm meter, but it is easier to measure using a surface voltmeter.) For powder deposited by either the corona or tribo-gun method, it sticks to the workpiece entirely by the image charge, but before it touched the piece, corona-deposited powder is attracted to the workpiece from a much longer distance away than is tribo-gun-deposited powder. Therefore, a smaller fraction of the powder from a tribo-gun actually reaches the workpiece. However, the tribo-gun powder coats more uniformly everywhere on the workpiece.
In both coating systems, the workpiece is often grounded. The coating problems discussed above (nonuniformity with corona and poor efficiency with tribo) can be largely corrected by applying a bias voltage to the workpiece instead of grounding it. With a tribo system, this bias voltage is of the opposite polarity of the (usually positive) powder; that is, the workpiece is usually connected to a negative voltage when bias is used. This connection increases the distance over which the powder is attracted to the workpiece, but it also somewhat decreases the coating uniformity. There is an optimum bias voltage, usually around -5 kV, which balances efficiency with uniformity. For a corona system, a bias voltage that is of the same polarity as the powder will improve uniformity. (This is also usually a negative bias voltage, in the range of -3 kV). The bias voltage in a corona system has the opposite effect of bias in a tribo system: corona system bias decreases the efficiency while increasing the uniformity, but again there is an optimum voltage.
There are some things to be aware of when using bias. The bias should be turned off (and the workpiece grounded) as soon as possible after coating. If the bias (high voltage) remains connected, some of the powder may quickly acquire charge and fly away from the workpiece. The deposition area should be kept clean and free of any grounded conductors or contaminants that may come close to the workpiece or the bias wiring. These may arc and reduce the bias voltage (immediately reducing the coating quality) or eventually burn out the bias voltage supply. The use of bias on the workpiece voltage is a relatively new concept; this option may not have been available when your system was purchased. If there are problems as above, check with the coating system manufacturer to see if an add-on bias voltage supply is available. (AlphaLab does not currently manufacture bias voltage supplies, but if you have trouble finding one for your system, email us at mail@trifield.com for suggestions.
Although electrostatic deposition can coat the back side of the workpiece, the backside coating is usually thinner than the front (the side nearest the sprayer). External air circulation can be adjusted to force more of the particles around to the back. With a corona system, an additional high-voltage needle can be added. It should be positioned to shoot ions and charged paint toward the back side. The corona process works most efficiently in a limited range of relative humidity (usually 45-60%).
Problems occur if the corona discharge system becomes dirty or does not function properly because of humidity or an improper voltage supply. Also an arc can occur under certain circumstances. If solvent-based paint is being applied instead of powder, it may be ignited if the arc energy is above about 1/4 millijoule. Powder may ignite with a spark that has energy of at least 5 millijoules. The workpiece must be conductive and grounded: if the workpiece is an insulator, special preparations must be carried out. Certain materials like wood, stone or even glass can be made conductive enough to be sprayed, at least when the humidity is high enough. Unfortunately, a high underlying water content may degrade the durability of the surface. Also the corona process works most efficiently in a limited range of relative humidity (usually 45-60%). It’s also necessary to spray these poorly-conductive workpieces at a slower rate, to avoid charging up regions of the surface. (These materials discharge only slowly to ground). If the workpiece is non-conductive, it can be conventionally painted first with a conductive primer. An insulator can also be electrostatically sprayed if it is very thin and is backed by a grounded conductor.
Problems with the coating can be diagnosed. It is a good idea to have a way of measuring both the total amount of paint or powder being dispensed per second and the total DC current carried by the spray. These two variables are not necessarily correlated. The amount of paint/powder per second is a measure of how well the atomizer or nozzle is working, but if the particles are not sufficiently charged, they will not be effectively attracted to the workpiece. The spray rate can be measured by briefly placing a thin grounded metal sheet in front of the sprayer for a pre-determined amount of time (e.g., one second). Then the thickness change or weight change can be measured. The current of the spray can be measured with a microamp meter connected between the workpiece and ground, so that after the current from the particles is transferred to the particles, it passes thorough the microammeter and then to ground. When the system is properly working, establish a baseline current (typically around 100 microamps). If the current drops over time, you may want to clean the corona discharge assemble and/or increase the voltage. The current can instead be measured at the same time you do a test of the spray rate, by connecting the microammeter between the thin metal sheet and ground.
If there are coverage problems on the workpiece, it may also be caused by a poor ground connection or a bad connection to the workpiece bias voltage. Check the ground connection with an ohm meter to a known ground (like a metal plumbing pipe of a metal conduit. It should be less than 1000 ohms (1K ohm). If the workpiece is a material that’s usually a poor conductor, you can measure the surface resistance (which should be done while the sprayer is off). This should be measured in a region of the workpiece that is generally observed to have the poorest coverage. Surface resistance should be on the order of 10 Meg ohms (10M ohms) per square or less. If it reads more than that, coat the workpiece with conductive paint (by conventional dip, brush, or spray painting). There are various manufactures of conductive paint, which usually contain copper, nickel and/or silver powder. A much less expensive paint uses graphite.
Surface Conductivity: It is often necessary to make surfaces at least slightly conductive. The magnitude of conductivity depends on the application, and this magnitude is usually measured in “ohms per square.” (Technically, an ohm is a unit of resistance, which varies inversely with conductivity. A high number of “ohms per square” means that the surface has low conductivity. Because ohms are a familiar concept, the rest of this section will use ohms in quantifying how “conductive” a surface is.)
The “ohms per square” resistance measurement of a surface is usually done by connecting the two wires of an ohm meter to the surface in a particular way. (For anti-static measurements, a very high-resistance ohm meter is required. For even higher resistances, direct “ohms per square” measurements are difficult, and alternative methods are described here.) If two wires are touched to the surface at random locations, a certain number of ohms will be measured. If the spacing between the two wires is increased, the number of ohms will be higher. If the tips of the wires are replaced by wide discs, the area of each contact will increase. This will decrease the number of ohms displayed on the meter. Obviously, some way of standardizing the measurement must be devised. The standard method is the “ohms per square”. With this method, a square sample of surface is removed (however in practice there is an equivalent method that does not require cutting the surface). Then conductive paint is applied to two opposite sides of the square as shown below, and the two wires are connected to the ohm meter. (Assume that only the top surface, where the conductive paint is applied, is conductive.) If the square is 1 X 1 inch, a certain number of ohms will be read. If a new square that is 5 X 5 inches is removed from the sample, it will read the same number of ohms as the 1 X 1 inch sample. In fact, any square of the same material, when measured in this way will read the same number of ohms regardless the size of the square.
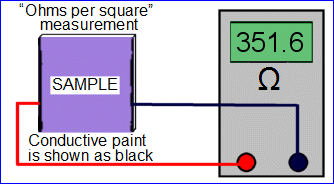
In some cases an extremely conductive surface is needed (less than about 10 ohms per square). This kind of surface may be required to carry significant electric current to discharge static very quickly, or to shield enclosed electronics from outside interference. These surfaces are usually metal or coated with metal paint (containing a significant amount of nickel, copper, or silver powder in a polymer binder and solvent). Metal paints are expensive and must be mixed constantly while painting; otherwise, the metal powder settles to the bottom of the painting container. A much less expensive conductive paint can be made with a mix of graphite powder, a plastic paint vehicle (such as ABS or polystyrene), and solvent (such as xylene and/or acetone). Very fine-ground graphite (5-10 micron) works best. This type of paint does not require constant mixing because graphite is much lighter than metal, but it is somewhat less conductive. (Contact AlphaLab for paint recipes.)
Surfaces that only need to be static-dissipating can be made of a wider variety of materials. Glass, cotton, wood, concrete and paper are slightly conductive, and the conductivity depends on humidity. A surface with a trillion ohms (=1000 gigohms or a million megohms) per square may be considered just barely static-dissipating. Less resistance is of course better. Glass, wood, concrete and paper generally achieve that at 40% or higher humidity. (For the relationship between ohms per square and static discharge time, click here.) Some types of spray paint are slightly conductive. As of this writing, Krylon brand “BBQ & Stove” black paint is a good permanent antistatic spray paint with about a billion ohms per square (although its formula has changed over time– earlier batches were insulating).
In order to remove static, at least one part of a conductive or anti-static object must be connected to earth ground. Without this connection, if the object becomes charged with an excess of either + or – , nothing could dissipate the charge except for air ions naturally present. (This natural-ion discharge typically takes 10 to 100 minutes for the object’s charge to be reduced to one half. If a lot of radon or other radioactive material is present in the air, more ions will be present and the discharge will be faster.) Ionizers will add ions to the air and create much faster discharge times, as further discussed here.